Residential Construction Delays: Expert Insights to Navigate Challenges and Stay On Schedule
For homeowners and builders alike, residential construction delays can derail timelines, inflate budgets, and strain relationships. With the average U.S. home build taking 7–12 months due to factors like supply chain disruptions and labor shortages (U.S. Census Bureau, 2023), understanding how to mitigate delays is critical. This guide, crafted by industry professionals with over 15 years of experience in construction management, unpacks the top causes of delays and actionable strategies to avoid them.
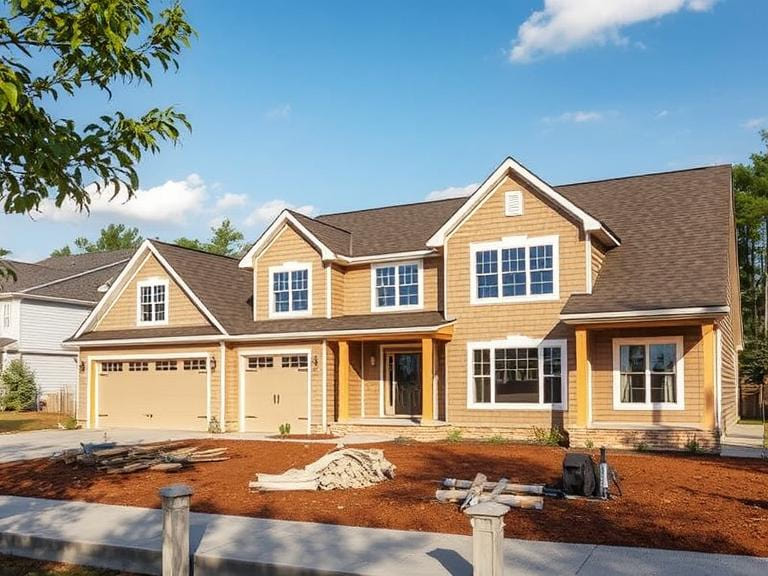
Why Residential Construction Delays Happen (And How to Prevent Them)
1. Budget Conflicts: Balancing Costs Without Compromising Quality
Budget overruns plague 90% of residential projects, often due to fluctuating material prices or design changes mid-construction. For example, lumber costs surged by 300% in 2021, catching many homeowners off guard.
Expert Solution:
- Adopt fixed-price contracts with builders to lock in costs.
- Allocate a 10–15% contingency fund for unexpected expenses.
- Use tools like Procore or Buildertrend for real-time budget tracking.
2. Poor Construction Planning: The Domino Effect of Inefficiency
A lack of detailed planning leads to missed deadlines. One 2023 survey found that 68% of delays stem from inadequate scheduling.
Expert Solution:
- Implement Building Information Modeling (BIM) to visualize timelines and identify clashes early.
- Hire a certified construction manager to oversee Critical Path Method (CPM) scheduling.
3. Design Issues: Avoiding Revisions That Derail Progress
Last-minute design changes account for 35% of delays, according to the American Institute of Architects. A common pitfall? Overlooking local zoning laws, which can force costly redesigns.
Expert Solution:
- Involve contractors in design reviews using collaborative platforms like AutoCAD or SketchUp.
- Conduct a feasibility study with architects before breaking ground.
4. Inaccurate Engineering Estimates: Bridging the Expectation Gap
Misjudging site conditions (e.g., unstable soil) or labor hours can extend timelines by months. A 2024 ASCE report highlights that 40% of residential projects underestimate excavation complexity.
Expert Solution:
- Partner with licensed engineers for geotechnical surveys.
- Compare estimates against historical data from similar projects.
5. Poor Communication: Aligning Stakeholders for Success
A National Association of Home Builders study found that 52% of delays arise from miscommunication between builders, subs, and clients.
Expert Solution:
- Schedule weekly check-ins via tools like Microsoft Teams or Slack.
- Designate a lead point-of-contact to streamline updates.
6. Subcontractor Challenges: Vetting Reliable Partners
Labor shortages have made subcontractor scheduling a top concern. In 2023, 60% of builders reported delays due to sub no-shows.
Expert Solution:
- Pre-qualify subs using platforms like Construction Monitor to verify licenses and reviews.
- Include penalty clauses in contracts for missed deadlines.
7. Material Shortages: Overcoming Supply Chain Volatility
Material shortages and manufacturing delays have become a critical pain point in residential construction, exacerbated by global supply chain disruptions. For instance, the National Association of Home Builders (NAHB) reports that as of 2023, 90% of builders faced delays due to shortages of appliances, roofing materials, and windows, with lead times stretching up to 6 months for items like electrical transformers. These bottlenecks often stem from geopolitical tensions, trade restrictions, or labor strikes at ports—factors beyond a builder’s control.
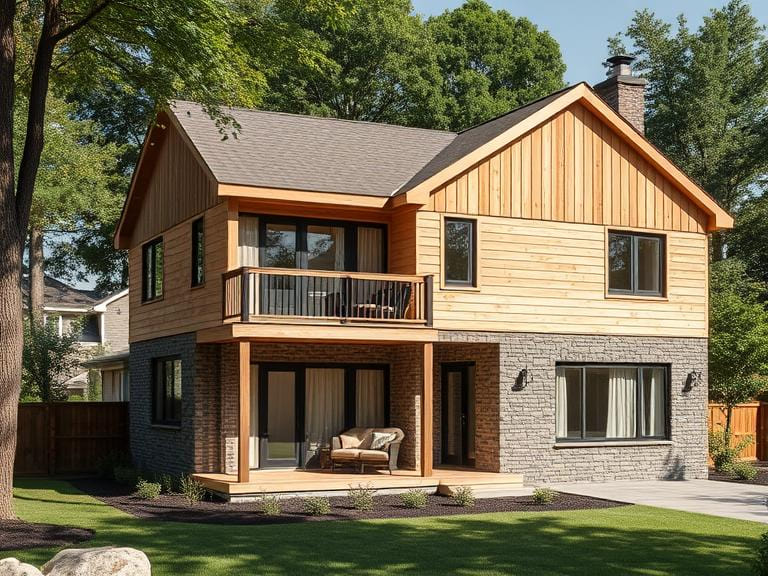
Advanced Solutions for Modern Challenges
To combat these hurdles, proactive builders are adopting innovative strategies:
- Diversified Sourcing: Partner with multiple suppliers across regions. For example, after Hurricane Katrina, builders in the Gulf Coast began sourcing lumber from both Canadian and South American providers to mitigate regional climate risks.
- Prefabricated Materials: Modular construction, where components are factory-built and shipped ready-to-install, cuts on-site delays. A 2024 Dodge Construction Network study found that prefab projects finish 30% faster than traditional builds.
- Just-in-Time Ordering: Tech tools like InventoryLink sync material orders with project milestones, reducing storage costs and theft risks.
Case Study: Local Sourcing Success
In Austin, Texas, a custom homebuilder avoided a 4-month delay for imported tiles by switching to locally quarried limestone. Not only did this keep the project on schedule, but it also reduced carbon emissions by 15%, appealing to eco-conscious clients.
Regulatory Preparedness
Stay ahead of trade policies by subscribing to alerts from the U.S. International Trade Commission. For example, tariffs on steel imports in 2023 prompted savvy builders to stockpile materials pre-announcement, sidestepping 20% cost hikes.
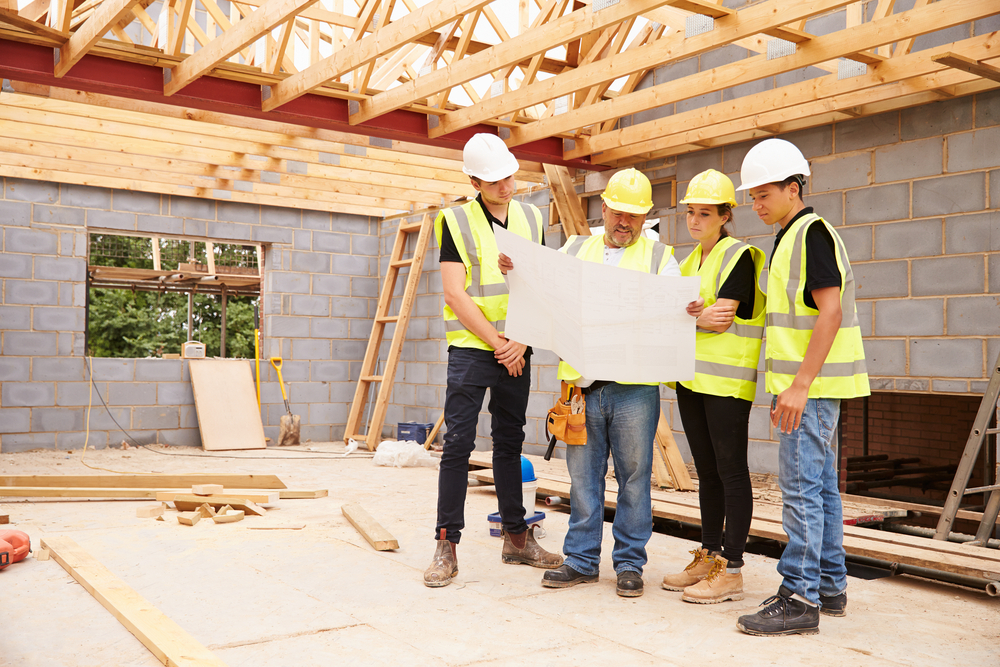
Proactive Measures to Minimize Delays
- Leverage Technology: Tools like CoConstruct integrate budgeting, scheduling, and communication in one platform.
- Legal Safeguards: Include force majeure clauses to address unforeseeable delays (e.g., extreme weather).
- Homeowner Involvement: Regularly visit the site and request progress photos to stay informed.
Conclusion: Turning Knowledge Into Action
Residential construction delays are costly but avoidable. By prioritizing detailed planning, transparent communication, and contingency strategies, homeowners and builders can keep projects on track. For further guidance, consult resources like the National Association of Home Builders or hire a certified construction consultant.
Find Us on Socials